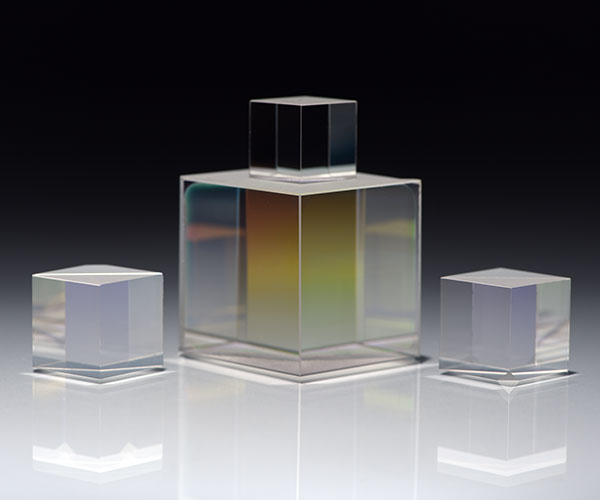
- Industry competing laser damage thresholds
- Coatings for -ns to -fs pulsed lasers, as well as CW
- Hybrid IAD coatings available that balance high LIDT with environmental stability
High Laser Damage Coated Optics Selection
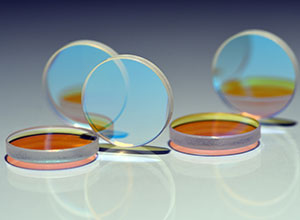
High Laser Damage Windows
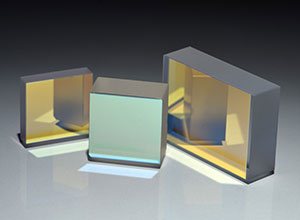
High Laser Damage Mirrors
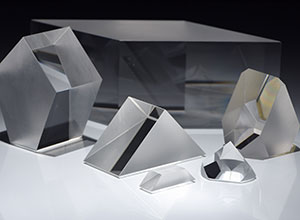
High Laser Damage Prisms
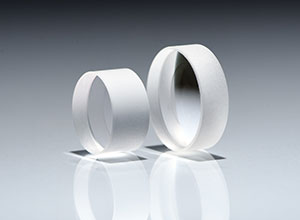
High Laser Damage Lenses
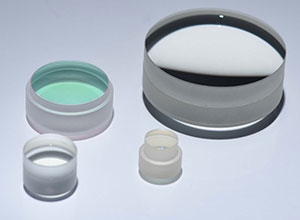
High Laser Damage Assemblies
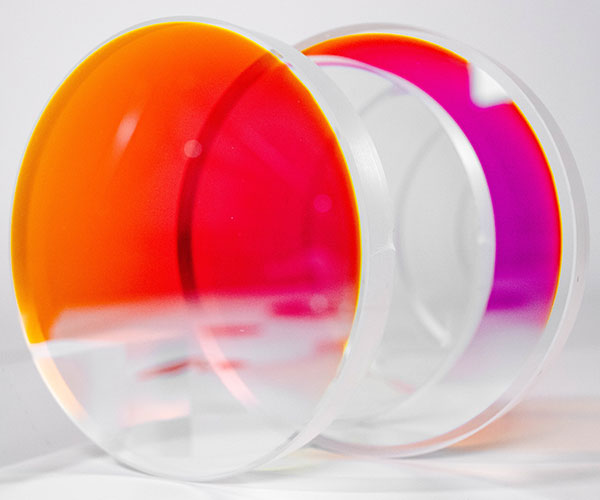
High Laser Damage Mirrors
High laser damage mirror coatings are extremely important in the laser industry. These mirrors are used to direct laser energy and are often times the coating of interest in the field of high laser damage coatings. PFG participates in the latest laser damage research and routinely has our coatings LIDT tested to ensure we provide our customers with the highest possible laser damage thresholds. We employ best-practice design techniques such as electric field optimization and half-wave protection layers to produce mirrors with maximum LIDT capability. We tailor our processes to the specific wavelength, pulse width, and repetition rate or CW parameters of our customer’s needs. Our E-beam coatings routinely provide some of the best -ns-pulse-width LIDT results in the industry. We also have the capability to provide ion-assist for -ps and -fs pulsed lasers, where higher energy processes provide higher LIDT. In addition, we provide hybrid E-beam and IAD mirrors, which strike a balance between LIDT, bandwidth, and environmental stability.
High Laser Damage Windows and Lenses
Despite the claim that coatings are the weakest link when producing laser-quality transmissive optics like windows and lenses, the substrate is equally as important as the coatings. Since the laser energy must traverse the substrate surfaces and bulk as well, the quality of the surface polishing, preparation, and cleaning becomes extremely important. PFG, having both polishing and coating capabilities, has the unique ability to control both substrate and coating quality to produce the highest-quality laser windows and lenses. Performed in our Class 1000 clean room, cleaning techniques such as spin-cleaning and optimized coating processes produce minimal defects, which are potential sites for failure. Coupling polishing processes and results, such as scratch/dig and surface roughness, with coating processes puts us in the position to outperform our competitors in quality and lead time. These high laser damage windows and lenses routinely provide our customers with longevity in some of the toughest laser environments in the field or lab.
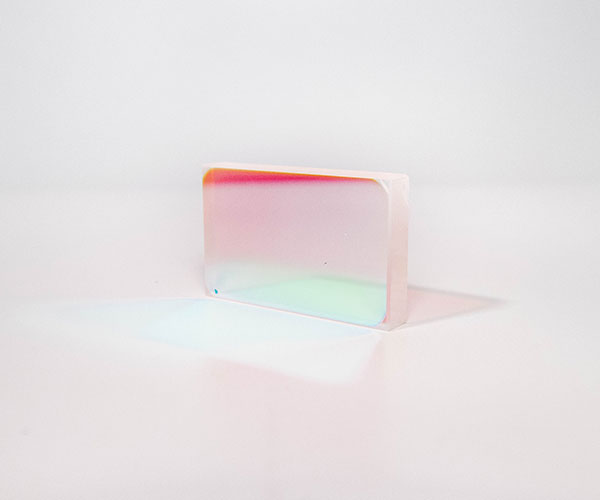
High Laser Damage Prisms
Laser alignment and steering are sometimes made much simpler with prisms instead of mirrors. Retroreflectors, 90° reflectors, and steering prisms (such as corner cubes, pentaprisms, and Risley prisms, respectively), for example, can all be used for steering and alignment without the need for mirror coatings. PFG fabricates these high-quality prisms and applies our high laser damage V-coat style laser line AR coatings to the entrance and exit faces. This allows for high-power beam steering when alignment is sensitive and critical.
CUSTOM LASER DAMAGE COATINGS
Our sales and engineering team will review your optical drawing or custom specifications and provide an estimate. Typically, we offer:Specification | Limit |
---|---|
Size: |
3 to 400mm |
Surface roughness: |
15Ǻ with the ability to provide below 5Ǻ if requested |
Surface quality: |
60/40 standard down to 10/5 Laser Quality (scratch/dig) |
Diameter: |
±0.05mm down to ±0.010mm |
Center Thickness (CT): |
±0.1mm down to ±0.025mm |
Clear Aperture (CA): |
85% down to 0.5mm or more from the edge of the finished optic |
Lens Centering: |
0.01mm ETD or 1 arc-minute deviation; 0.003mm ETD or 10 arc-seconds deviation |
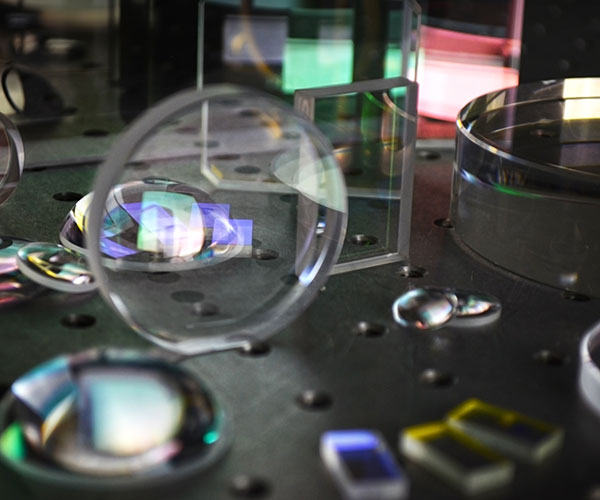
Optical Thin Film Coating Department Capabilities
- Specialize in producing custom coatings to meet customer specifications
- Electron Beam (E-Beam) and Ion-Assisted (IAD) coating process technologies
- Laser Line Coatings, Anti-Reflection, Highly Reflective, V-Coats, Broadband, Metallic, Polarizing, Non-Polarizing, Beamsplitters, Long-Pass Filters, and Short-Pass Filters
- Ultra-broadband AR’s available – covering visible and infrared (ex. 400nm – 2µm)
In-house environmental testing: adhesion test, abrasion test, thermal-humidity test, temperature influence test, and stress test. Coating charts and witness samples are routinely supplier